Quick Contact
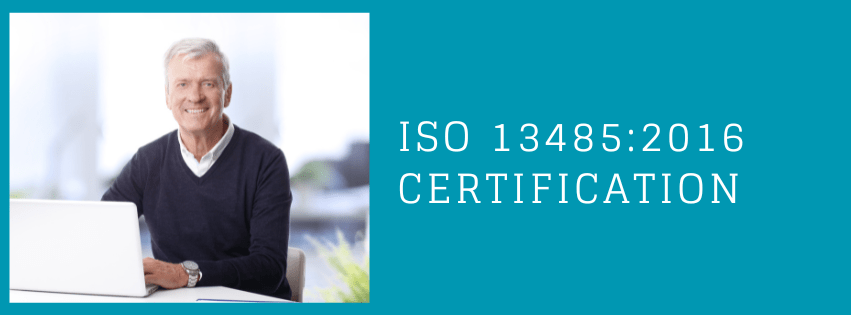
ISO 13485 Certification
ISO 13485 certification is essential for medical device companies that want to demonstrate compliance with regulatory standards at local, regional, national, and international levels. Following an on-site audit, the certification body issues medical device manufacturers an ISO certificate. Most medical device manufacturers qualify for ISO 13485 with a CE Marking Audit. Request ISO 13485 Quote.
A medical device quality management system, is a collection of policies, processes, documented procedures, and records that must be followed by a company by a set of internal rules tailored to the organizational needs of the product or service you provide to customers and patients.
Various countries accept BS/EN/ISO 13485 Certification. The latest version of the standard followed is (EN) ISO 13485:2016, published on 1st March 2016. The ISO 13485 standard is made to suit medical device manufacturers and or related industries /service providers to follow appropriate systems to practice and strengthen their risk management and regulatory overview.
(Listen for 4 Minutes)
ISO 13485 Certification For Medical Device and In-vitro Diagnostic Device Manufactures
ISO 13485 provides a competitive market advantage for medical device and in-vitro diagnostic manufacturers by boosting confidence among buyers and investors, thereby enhancing business opportunities. Many multinational medical device companies and suppliers prefer working with ISO 13485 certified firms to ensure compliance and quality.
ISO 13485 Certification for medical devices enables companies to establish a quality management system in all stages of product realization, including device design, development, manufacturing and production, servicing, installation, and market surveillance. The benefits of being an EN ISO 13485 Certification Companies are the following:
- ISO 13485 ensures the device consistently meets regulatory, safety, and performance from its initial design phase through to manufacturing, followed by distribution, and post-market surveillance.
- Ensures better supplier control, reducing risks associated with component quality and regulatory compliance.
- Many tenders and contracts require ISO 13485 Certificate. Companies without it may be disqualified from bidding.
- Ensures medical device safety and continual device improvement.
- Builds confidence among buyers and investors, enhancing business opportunities.
- By delivering reliable, safe, and quality medical devices, manufacturers can build strong relationships with healthcare professionals and healthcare facilities.
- Ensures a robust quality management system (QMS), reducing the likelihood of compliance violations, recalls, and penalties.
- ISO 13485 Certificate holders are more attractive to suppliers and distributors because they assure quality and regulatory compliance.
- ISO 13485 helps maintain a strong brand reputation in the market.
- Facilitates entry into strategic alliances, OEM agreements, and supply chain partnerships
Would you like to know more about our 13485 Certification services? Submit your email below for a quick response in minutes. Privacy Policy>
ISO 13485 Certification Process
Planning ISO 13485 certification for medical devices, organization involves a phased approach. Start by conducting a gap analysis by an expert lead accessor/auditor with good knowledge of medical device regulation. This helps identify areas that need improvement covering missing documentation and records, employee awareness, facility drawbacks etc.
Followed by creating an ISO implementation team with well-defined duties, responsibilities and authorities and above all a dedicated individual to oversee implementation and certification activities. Develop a project implementation strategy as shown in the below image with clear timelines, milestones, and resources needed.
Once the MD QMS is implemented conduct internal audits to identify any GAPS further before scheduling an audit with a certification body accredited with IAF. Top-level meetings with MR should be scheduled regularly to monitor progress.
Finally, once the QMS is ready invite a certification audit team, where the team will assess your system against ISO 13485:2016 requirements. Once completed the ISO 13485 certificate is granted.
Relationship Between ISO 13485 and ISO 14971
The relationship between ISO 13485 Certification and ISO 14791 is that both standards work together to establish an effective QMS. ISO 13485:2016 Section 4.1.2 b states that “apply a risk-based approach to the control of the appropriate processes needed for the quality management system.” This organization should adopt a risk-based approach to every process that affects quality.
ISO 13485:2016 Certification (QMS) focuses on the regulatory and customer requirements of medical devices. As a part of this, QMS requires risk analysis to be done, keeping ISO 14971 as the guidance document. This means ISO 13485 looks to ISO 14971 for guidelines for risk analysis and implementing risk control measures, thus ensuring the safety of the device during the product lifecycle.
Relationship Between ISO 13485 and IEC 62304
ISO 13485 is an exclusive standard that provides a QMS standard for the medical device industry. Software devices falling under Medical or Invitro devices must implement the requirements for the medical device software development cycle known as IEC 62304. The IEC 62304 standard may be implemented in conjunction with 13485 and offers a platform to suit and develop strategies for the software life-cycle processes, software development, and software maintenance.
As a basic platform, IEC 62304 assumes that medical device software is developed and maintained within a QMS such as ISO 13485 but does not require an organization to be certified in ISO 13485. Therefore, IEC 62304 can be a supplement to the 13485 standard.
ISO 13485 Implementation Process
Not all organizations are the same; some make class I medical devices, some make class III medical devices, and some manufacture IVD devices. Implementation of ISO 13485 Certification and its requirements are different from organization to organization. Generally, the following are the major stages of ISO implementation:
-
- Understanding the standard requirements
- Gap analysis of the current system and the requirements
- Stage wise planning of the QMS establishment
- Providing the required training for the QMS team
- Documentation of the QMS, including the records
- Internal Quality Audits and CAPA
- Management review meetings
Effective implementation is followed by continuously monitoring and measuring the processes to ensure they are effective. Take corrective actions for any non-conformities, address any issues and raise CAPA. Regularly review the Quality Management System to ensure the system remains effective and make improvements as necessary. By following these steps, you can effectively implement the system and achieve ISO 13485 certificate.
We are ISO 13485 Consultants and medical device regulatory experts for MDR, IVDR and FDA. We guide and understand the organization’s requirements in line with the product compliance team for proper implementation.
Frequently Asked Questions
Does compliance to ISO 13485 Certification demonstrate GMP?
Yes. 21 CFR 820 is also called GMP for medical devices. Its equal to ISO 13485 Certification.
What countries require ISO 13485 Certification?
- Europe – All countries accept (EN) ISO 13485:2016
- UK – BS ISO 13485:2016
- Canada – CAN/CSA-ISO 13485:2016
- USA – QMSR (21 CFR 820+ISO 13485)
- Japan – ISO 13485
- Australia – ISO 13485:2016
- ASEAN countries (Taiwan, Korea, Singapore, Malaysia, Philippines) – ISO 13485
- Latin America – ISO 13485
- India – ISO 13485
- Middle East – All countries accept ISO 13485:2016
Is there any guidance on the implementation of ISO 13485:2016?
Manufacturers or any organization planning to implement ISO 13485, may refer to ISO/TR 14969. (Note: It is not updated to suit ISO 13485:2016 currently, but still, all can use this guide)
What is the date of withdrawal for ISO 13485:2003?
The earlier version of the ISO 13485:2003, and the European version, EN ISO 13485:2012, standards were withdrawal on February 28th, 2019, providing a three-year transition period.
Who issues ISO 13485 Certification?
The ISO 13485 Certificate is issued by the Certification Body (CB or Registrar) after conducting audits on site with the latest version of the ISO 13485 standard.
How long it will take a certification body to issue ISO 13485?
Once the application with CB is finalized and the applicant is ready to be invited for an onsite audit, the certificate will be issued in 30 days to 45 days.
How ISO 13485 Certification Audit man-days are calculated?
ISO 13485 onsite audit days are calculated on the following factors
- Number of permanent employees
- Number of departments
- Number of products manufactured
- Design and development scope
- Cleanroom and sterilization activities
Is it compulsory to obtain ISO 13485 Certification for your organization?
No, having an ISO 13485 Certification is not mandatory unless requested by your vendor(s). However, as a responsible organization, you should implement ISO 13485 to the fullest extent.