Quick Contact
Very useful for small and medium size medical device manufactures
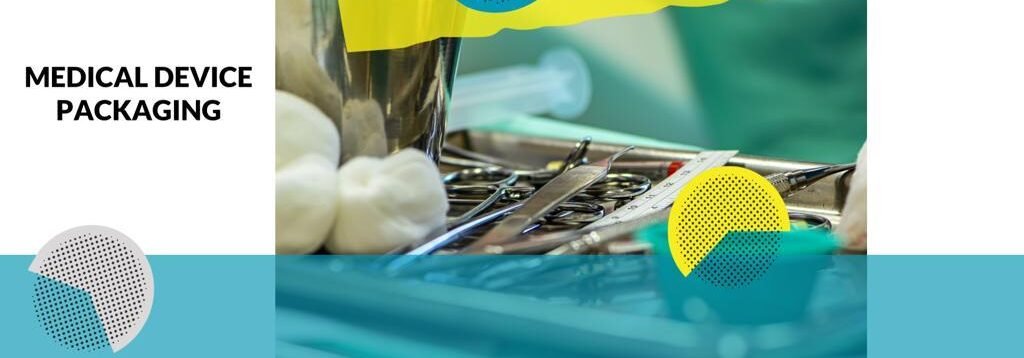
Medical Device Packaging
The integrity of medical device packaging, whether in pouches, trays, or blister packs, is crucial for maintaining the sterility of the enclosed devices throughout their journey from packaging to shipping, storage, and transportation to the hands of the user. This is been audited and reviewed by regulators during the file review. “Has the manufacturer taken the necessary level of care and sterilization for each batch or lot they manufactured?”
There are many kinds of medical device packaging materials and methods available. The material which comes in direct contact with the medical devices is known as primary packing material and the material which comes contact with the primary pack is called secondary packing this may be a paper/cardboard box.
For the bulk storage and for transportation tertiary packing system can be used, this may be a carton box. Thus, the main goal of packaging validation is to confirm the material and method used for the primary packaging of the device, which is suitable and yields the requirements of packaging. For example, the packaging material should be compatible with the sterilization process.
Interested to know more about MDR CE Marking? Submit your email for a quick response.
Medical Device Packaging Standards
Given the FDA’s and EU MDR / IVDR stringent standards for the sterility of approved medical devices, manufacturers are required to undergo thorough testing to demonstrate a package’s resistance to environmental factors that could compromise the contents’ sterility. This medical device testing is essential to demonstrate no potential threats posed during transport and aging of the packaging material, which may weaken over time and expose the contents to pathogens.
To meet these rigorous regulators requirements, medical device packaging covering packaging material, packaging process and packaging equipment’s must undergo a spectrum of validation tests, if applicable to prove its ability to withstand various environmental factors. These tests include bubble-emission and burst testing, among others as per ASTM or ISO 13485 Certification.
CE & 510k Requirments for Medical Device Packaging
Medical device packaging must comply with the Quality System Regulation standards (QSR 21 CFR 820), which outlines general controls for the design, manufacturing, packaging, labelling, storage, and distribution of medical devices. Packaging materials should be biocompatible, and the testing must be conducted by the ISO standard 10993-1:XXXX
If the medical device requires sterilization, the packaging must be designed to maintain sterility. Sterilization processes and validations are regulated by the FDA (21 CFR 880.6860). The packaging process must be validated (21 CFR 820.130) to ensure that it meets its intended purpose and does not compromise the safety and effectiveness of the medical device.
We provide ISO sampling guidance as per the EU MDR CE Marking, EU IVDR CE Marking, US FDA 510K and ISO 13485. Contact us for more information or fill out the form for a detailed quote
EU MDR /IVDR Medical Device Packaging Requirements
The EU has implemented the Medical Device Regulation (EU MDR 2017/745), which sets out requirements for medical devices, including packaging. The MDR emphasizes the importance of ensuring the safety and performance of medical devices throughout their lifecycle. The CE marking process involves conformity assessments, and the packaging is an integral part of this assessment.
The ISO 11607 standard specifies requirements for the development and validation of processes for packaging medical devices. Compliance with ISO 11607 helps demonstrate conformity with essential requirements. Similar to the FDA, the EU requires compliance with ISO 10993-1:XXXX for the biological evaluation of medical device packaging materials.
If sterilization is required, the packaging must comply with ISO 11135, which specifies requirements for the validation and routine control of ethylene oxide sterilization processes. EU MDR 2017/745 annex I GSPR, specifies the packaging requirements of medical devices. The requirements can be summarized as;
- The medical device shall package in a way that its characteristics and performance should not adversely affect during transport and storage.
- The medical device shall package in such a way as to minimize the risk posed by contaminants and residues to patients.
- The package shall ensure that retain the sterile condition, till the pack is broken.
- Packaging systems for non-sterile devices shall maintain the integrity and cleanliness of the product.
Medical Device Packaging Regulations
- EN ISO 11607-1 Addressing packaging materials, sterile barrier system.
- EN ISO 11607-2 Addressing validation of packaging processes.
- BS EN 868-2 Packaging for terminally sterilized medical devices. Sterilization wrap. Requirements and test methods
- ASTM D3330 Package Strength Testing by Peel Adhesion Testing
- ASTM F88 Package Strength Testing by Seal Peel Testing
- ASTM F1140 Package Strength Testing by Burst Testing
- ASTM F2054 Standard Test Method for Burst Testing of Flexible Package Seals Using Internal Air Pressurization Within Restraining Plates
- Package Integrity (ASTM F2096: Bubble Test)
- Seal Integrity (ASTM F1886: Visual Inspection, ASTM 1929: Dye Test)
- Seal Strength (ASTM F88: Peel Test, ASTM F1140: Burst Test)
FDA and NB expected Documentation and Reports
For terminally sterilized medical devices , the validation process involves creating a validation plan, that shall contain the following.
- Document ID, Date of revision, Issue and Responsibilities,
- Description of the materials
- Description of equipment
- Skilled Personnel
- How the packaging process going to carry out
- Description of sterilization process
The packaging process validation report shall document the following.
- The evidence of packaging process validation (result of IQ, OQ and PQ).
- Formal approval of validation along with Report ID, Report date
- Process Control and Monitoring
- Process changes and revalidation
Non-Sterile Product Packaging Requirements
Literally, there is no specific standard to follow for the medical device packaging validation of non-sterile medical devices. However, the manufacturer must fulfil the requirement of GSPR. Thus, it is up to the manufacturer to select appropriate packaging for their medical device, and it should not be harmful to the function and efficiency of the device.
The package must be sufficient to protect the device, for example, if a drop will damage your device, then the package must be sufficiently padded/cushioning form to protect the device damage from dropping.